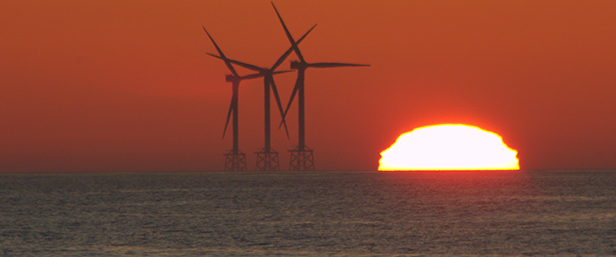
Seekabel
Für die Anbindung der Offshore-Windparks an das Übertragungsnetz werden Seekabel eingesetzt.
Die zu verwendenden Kabel sind grundsätzlich wartungsfrei. Lediglich im Fall eines selten vorkommenden Kabeldefekts kann es für die Reparatur notwendig werden, den schadhaften Kabelabschnitt auszuspülen. Um Beschädigungen von allen in der See verlegten Kabeln (zum Beispiel durch Schiffsanker, Bagger oder Fischfanggeräte) vorzubeugen, haben sich das Zusammenlegen von mehreren Kabeln zu Kabelbündeln (im Folgenden zum Begriff Kabel generalisiert), die Kennzeichnung der Route und das Einbringen der Kabel in den Seegrund als wirksame Schutzmaßnahmen bewährt. Entsprechend des Leitungsabschnittes werden die Kabel mit verschiedenen Überdeckungen und in verschiedenen Abständen zueinander und zu anderen Kabelleitungen arrangiert. Kreuzungen von Seekabeln untereinander sowie mit anderen bestehenden und geplanten Rohrleitungen oder Seekabeln sollen soweit wie möglich vermieden werden.
Die Übertragungsnetzbetreiber haben sich dazu entschlossen, die Windparks in Nord- und Ostsee mit Hilfe unterschiedlicher Techniken anzuschließen. In der Ostsee soll die Anbindung mit Wechselstrom erfolgen. In der Nordsee wird dagegen aufgrund der durchschnittlich größeren Entfernungen Gleichstrom genutzt. Deshalb werden dort eine weitere Plattform auf See und eine Konverterstation an Land benötigt.
Bauphase / Kabelverlegung
Bevor es in der Bauphase zur eigentlichen Kabelverlegung kommen kann, ist eine gezielte Trassenräumung von außer Betrieb genommenen Leitungen und eine generelle Räumung des Arbeitsbereichs durchzuführen, damit die Kabellegung und das Eingraben möglichst risikofrei erfolgen können. Dabei ist auch auf eine gegebenenfalls notwendige Munitionsberäumung zu achten.
Entscheidend für die Wahl des Verfahrens zur Kabelverlegung in der See ist neben der Wassertiefe vor allem die Beschaffenheit des Meeresbodens. Das jeweilige Kabel wird dabei zunächst auf dem Meeresboden verlegt und anschließend versenkt.
Um Einschränkungen unter anderem für die Schifffahrt und die Fischerei zu minimieren, wird ein zeitlich koordiniertes Verlegen und Eingraben von mehreren Seekabeln angestrebt. Die Verlegung von zwei oder mehreren Kabeln erfolgt dabei in einem oder mehreren Schritten, je nachdem ob die Kabel gebündelt oder einzeln vorliegen.
Die Kabel werden grundsätzlich parallel zueinander und zu bestehenden Infrastrukturen geführt. Die Mindestabstände sind dabei so zu wählen, dass eine thermische Entkopplung sichergestellt ist und kumulative Wärmeeffekte ausgeschlossen werden können. Die Parallelführung der Seekabel dient zusätzlich der Vermeidung von negativen Effekten auf die Meeresumwelt, weil dadurch die Einbringung künstlicher Kreuzungsbauwerke, insbesondere in Meeresgebieten mit überwiegend homogenen sandigen Böden, vermieden werden kann.
Die Seekabelverlegung erfolgt bei einer Wassertiefe von mehr als 10 m (Tiefwasserzone) mit einem sogenannten Dynamic-Positioning-Schiff. Im Bereich von etwa 10 m Wassertiefe bis zur Anlandung (sogenannte Flachwasserzone) wird die Seekabelverlegung mit einem Ponton bevorzugt.
Um die Kabelverlegung möglichst umweltfreundlich zu gestalten, sollten (unter Berücksichtigung der Belange unter anderem von Schifffahrt und Fischerei) die Seekabel nur so tief wie erforderlich und möglichst schonend verlegt werden. Dies vermeidet nicht nur einen umfangreichen Bodenaushub und eine erhöhte Beanspruchung des Sediments, sondern schützt auch beispielsweise den Siedlungsraum der benthischen Lebensgemeinschaften.
Die empfohlene Verlegungstiefe, also der Abstand von der Oberkante des Kabels bis zur Oberkante des Meeresgrundes, beträgt für die ausschließliche Wirtschaftszone 1,5 m, für das Küstenmeer 1,5 bis 3 m und für die Anlandungszone 1,5 bis 2 m. Der Mindestabstand zu anderen Leitungen sollte im Meer 100 m und in der Anlandungszone 20 m nicht unterschreiten. Das Versenken der Seekabel in den Meeresboden ist grundsätzlich mittels Pflügen, Vibrationspflügen, Fräsen, Einspülen und Horizontalbohrung möglich.
Neben der eigentlichen Seekabelverlegung muss auch das eventuelle Beheben von Defekten betrachtet werden. In der Regel wird bei einer technischen Störung der schadhafte Abschnitt recht genau lokalisiert, gezielt aufgesucht und dann gegen ein neues Stück Kabel mit zwei Kabelmuffen ausgetauscht. Bei der Reparatur potenziell auftretende Beeinträchtigungen sind äquivalent mit den oben aufgeführten baubedingten Auswirkungen.
Darüber hinaus ist auch auf den später anfallenden Rückbau der Seekabel zu achten, welche generell nach Aufgabe der Nutzung wieder entfernt werden müssen. Ausnahmen gibt es hier nur, wenn der Rückbau vergleichsweise größere Nachteile mit sich bringen würde.
Anlage
Im Bereich der Hoch- und Höchstspannung gibt es bei der Anlage von Seekabeln zwei unterschiedliche Typen: das sogenannte papierisolierte Kabel und das sogenannte kunststoffisolierte Kabel. Prinzipiell sind beide Kabeltypen ähnlich aufgebaut. Die elektrischen Leiter sind durch einen Stoff isoliert und durch einen Schutzmantel gegen mechanische Beschädigung geschützt.
Unabhängig von der Isolierung besteht der Leiter bei einem Seekabel in der Regel aus Kupfer (Aluminium wird eher bei Landkabeln eingesetzt) und besitzt einen Durchmesser von etwa 45 mm.
Das Gewicht eines Seekabels beträgt pro Meter etwa 44 kg. Aufgrund dieses hohen Kabelgewichts richtet sich die Länge der Seekabel nach der Ladekapazität des Verlegeschiffes.
Die jeweiligen Kabelteilstücke werden durch sogenannte Muffen miteinander verbunden. Darüber hinaus werden relativ aufwändige Kreuzungsbauwerke notwendig, sobald sich zwei Kabel kreuzen.
Im Gegensatz zu Wechselstromkabelsystemen ist es bei der Höchstspannungs-Gleichstromübertragungstechnik (HGÜ) grundsätzlich möglich, monopolare Kabelsysteme zu benutzen. Neu errichtet werden heute grundsätzlich nur noch bipolare Systeme, bei denen Hin- und Rückleiter ausgebildet sind. Daneben gibt es auch noch koaxiale Systeme.
Betriebsphase
In dem im Sediment am Meeresgrund verlegten Kabel kann es durch Übertragungsverluste zur Wärmeentstehung und damit zu einer Temperaturerhöhung kommen. Die Manteltemperatur der Seekabel kann dabei im Extremfall bis zu 70 °C betragen, die Temperatur im Leiter kann bei einer Überlastung sogar bis auf 90 °C ansteigen.
In welchem Ausmaß die Erwärmung des Kabels auch zu einer Erwärmung des Sediments unmittelbar am Kabelmantel führt, hängt zum einen von der Wärmekapazität, der Wärmeleitfähigkeit und der Temperatur des Sediments ab, zum anderen spielen aber auch der Kabeltyp sowie dessen Auslastung und ob es sich um ein Gleichstrom- oder Wechselstromsytem handelt eine entscheidende Rolle.
Im Durchschnitt ist unmittelbar am Kabel ein Temperaturanstieg im Bereich von 5 bis 15 K zu erwarten, unter ungünstigen Voraussetzungen kann aber auch mit einem Temperaturanstieg um bis zu 30 K gerechnet werden. Der entsprechende Wärmegradient umfasst mehrere Meter.
Bezogen auf die ausschließliche Wirtschaftszone (AWZ) wurde in 20 cm Sedimenttiefe ein maximaler Temperaturanstieg von 2 K als zulässig festgelegt. Für den küstennahen Bereich der Boddengewässer und des Wattenmeeres sollte der Temperaturanstieg im Sediment schon in 30 cm Tiefe 2 K nicht überschreiten. Für den küstennahen Bereich des Wattenmeeres und der Windwatten in der Ostsee muss außerdem beachtet werden, dass durch den Gezeitenwechsel eine ständige Wasserbedeckung teilweise nicht möglich ist. Eine Erwärmung des Wattbodens ist demnach während Ebbe deutlich wahrscheinlicher.
Während des Betriebs sind Störungen durch mechanische Einwirkung, Korrosion, Überspannung oder mechanisch-thermische Überbeanspruchung (Wärmeemissionen) möglich. Potenzielle Wirkungen können beim Betrieb von Seekabeln auch von Bränden und Explosionen der Endverschlüsse der Muffen ausgehen.
Nach derzeitiger Zulassungspraxis ist die Lage des Kabels der zuständigen Zulassungsbehörde in den ersten fünf Jahren der Betriebsphase jährlich durch jeweils mindestens eine Überprüfung der Tiefenlage nachzuweisen. Darauf folgend wird die Anzahl dieser Überprüfungen von der Zulassungsbehörde einzelfallbezogen festgelegt.
Quellennachweis für die hier zum Seekabel gemachten Ausführungen
Belli, S., Perego, G., Bareggi, A., Caimi, L., Donazzi, F., Zaccone, E.: P-Laser (2010): Breakthrough in power cable systems. Conference Record of the 1988 IEEE International Symposium. DOI: 10.1109/ELINSL.2010.5549826.
Bundesamt für Seeschifffahrt und Hydrographie (2013): Umweltbericht zum Bundesfachplan Offshore für die deutsche ausschließliche Wirtschaftszone der Nordsee 2012. Hamburg.
Bundesamt für Seeschifffahrt und Hydrographie (2013): Untersuchung der Auswirkungen von Offshore-Windenergieanlagen auf die Meeresumwelt (StUK4). Hamburg.
Bundesamt für Strahlenschutz (2013): Umweltauswirkungen der Kabelanbindung von Offshore-Windenergieparks an das Verbundstromnetz - Effekte betriebsbedingter elektrischer und magnetischer Felder sowie thermischer Energieeinträge in den Meeresgrund. urn:nbn:de:0221-2013022510313. Salzgitter.
Hofmann, L., Mohrmann, M., Rathke, M. (2012): Ökologische Auswirkungen von 380-kV-Erdleitungen und HGÜ-Erdleitungen. Bericht der Arbeitsgruppe Technik/Ökonomie. Auftraggeber: Bundesministerium für Umwelt, Naturschutz und Reaktorsicherheit (BMU). E. Cuvillier Verlag. 1. Auflage.
Hunke, D., Schüler, V. (Ecofys) (2009): Morphologische Stabilitätskarte für die Kabelanbindung von Offshore-Windparks in den Flussmündungsbereichen von Elbe, Weser, Jade und Ems - Endbericht. Auftraggeber: Bundesministerium für Umwelt, Naturschutz, Bau und Reaktorsicherheit (BMUB). Berlin.
IBL Umweltplanung (2012): Netzanbindung von Offshore-Windparks - Orientierungsrahmen Naturschutz für Anschlussleitungen im Abschnitt Seetrasse. Anlage 1 zu Teil 2: Effekte und Auswirkungen der Kabelverlegung - Arbeitshilfe Eingriffsregelung. Erläuterungsbericht. Oldenburg.
IBL Umweltplanung (2012): Netzanbindung von Offshore-Windparks - Orientierungsrahmen Naturschutz für Anschlussleitungen im Abschnitt Seetrasse. Teil 2: Begründungen und Erläuterungen. Erläuterungsbericht. Oldenburg. Seite 3.
Kegler, J.F. (2015): Anbindung von Offshore-Windparks, Leitungsverlegung in der Nordsee und im Wattenmeer. In: Energiewende und Archäologie. Deutsche Bundesstiftung Umwelt (Herausgeber). Osnabrück. Seite 32 ff.
Küchler, A. (2009): Hochspannungstechnik: Grundlagen - Technologie - Anwendungen. Springer Verlag, 3. Auflage. Heidelberg. Seite 477 ff.
Niedersächsische Landesbehörde für Straßenbau und Verkehr (2011): Planfeststellungsbeschluss für die Netzanbindung der Offshore-Windkraftanlage Riffgat mittels einer 155 kV-Wechselstromleitung der TenneT TSO GmbH Seekabelabschnitt: Transformator-Plattform des Windparks bis zum Anlandungspunkt nordwestlich von Pilsum. Hannover. Seite 6.
Niedersächsischer Landesbetrieb für Wasserwirtschaft, Küsten- und Naturschutz (2012): Kabelverlegungen ¬Anforderungen des NLWKN und der NLPV an Untersuchungen im niedersächsischen Küstenmeer sowie in Küsten- und Übergangsgewässern. Küstengewässer und Ästuare, Band 5. Norden.
Fachstellungnahme im Auftrag der Bundesnetzagentur (2012):
Gutachten zu Umweltauswirkungen unterschiedlicher Netzkomponenten (pdf, 1 MB)